
- #Stl to cnc usb controller drivers
- #Stl to cnc usb controller full size
- #Stl to cnc usb controller driver

The + output can is based on the voltage of the Limit switch input.

For each of the X, Y, Z, A, B, C Axis outputs there is a 5V, Enable, Step and Direction lines.These allow for custom made cables to be simply pushed in and connected back to the motors and limit switches. It also has JST connectors for some of the I/O’s that are commonly used on a 3-Axis machine such as the D-500.
#Stl to cnc usb controller full size
To view the picture above in more details, you can right click and save the image or click on it and choose view full size from the bottom of the image frame.Īll the I/O’s have been been broken out to connector blocks and the PCB has legends next to each one. These I/O’s can be switched to to either configuration by simply setting a jumper or by connecting a single way switch. The controller board itself has a huge number of inputs and outputs to take full advantage of the features found the 6-axis GRBL firmware and the Mach3 interface. So all we need to do is supply power to each motor and data control lines from our controller board. along with an encoder that makes sure their are no lost steps and great performance.
#Stl to cnc usb controller driver
the Closed Loop Stepper motors have the driver built on on the motor.
#Stl to cnc usb controller drivers
We are supplying it with a branded, genuine MEAN WELL 36V 8.9amp power supply that has a wide range working voltage input of between 88V and 264V AC.Īs you can see there are no stepper drivers inside the controller box as we now use Closed Loop Stepper motors on all our machines. Both have power switches at the front of the box.

The whole box acts as a sturdy heat sink and helps keep everything nice and cool.Īlso their are two AC input sockets on the back, one for the main power supply and another for the spindle. The box itself is all made out of aluminium plates that have been finished with a black oxidisation and laser marked. Inside the controller box there is plenty of room to mount the controller as well as power supply and cables.
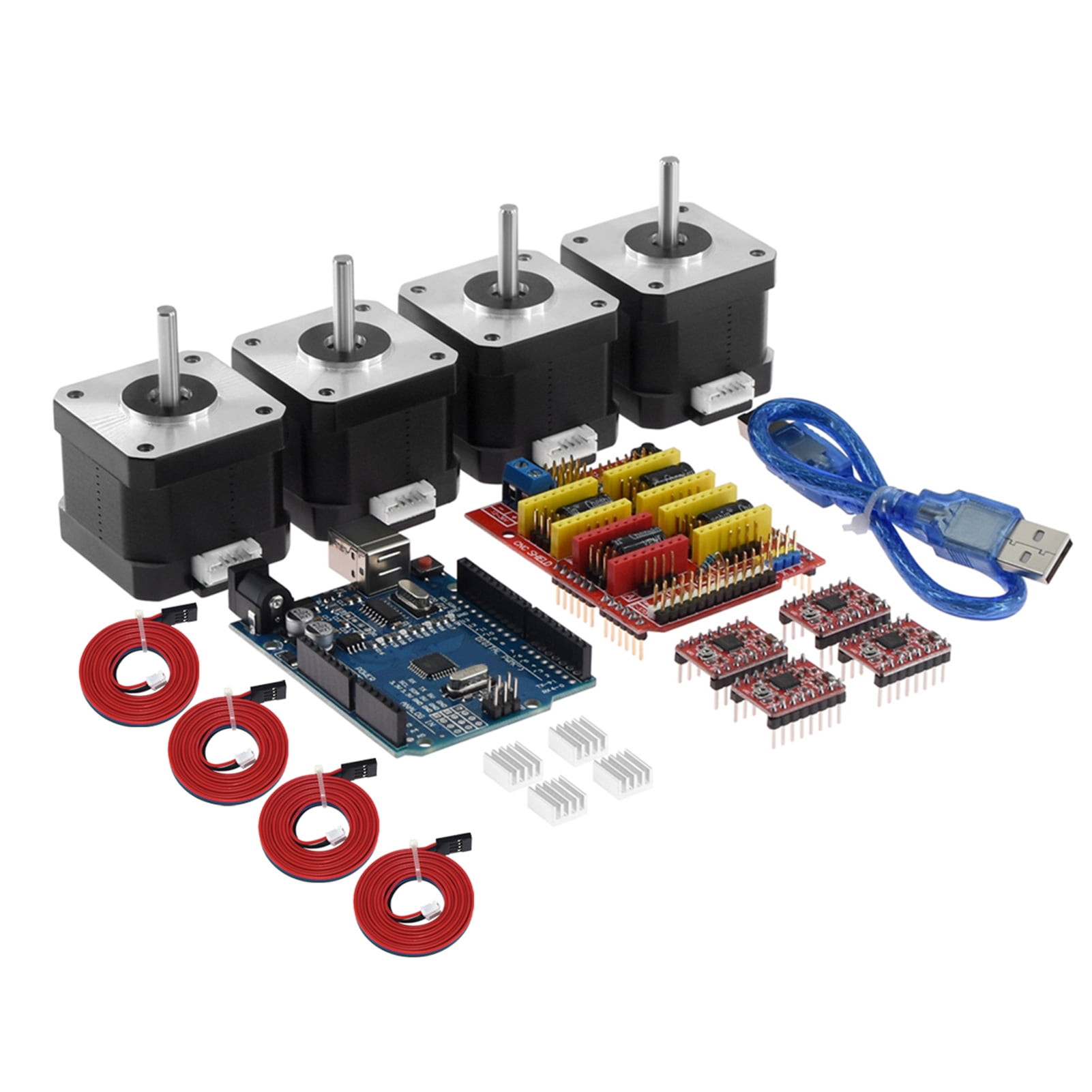
When mounted in our controller box that we designed, you can see you have easy access to the USB port, DC power input and parallel port. We have programmed the Arduino board with the Grbl-Mega-5X firmware which is open source and can be downloaded from the following linkĪs you can see in the picture above the main breakout board in the middle will plug into the Arduino Mega 2560 R3 board and then the board on the right plugs into the breakout board. Multiple limit trigger inputs that are all buffered and opto isolated along with a ARM processor that monitors the motor alarm lines. So best of both worlds for those wanting to experiment running their machines with different Gcode engines.īeing 6-Axis allows for future expansion of the machine.
